How Can SOLIDWORKS TolAnalyst Improve Tolerance Stack-Up Analysis?
- Get link
- X
- Other Apps
SOLIDWORKS TOLERANCE STACKUP ANALYSIS
The TolAnalyst tools that are built into SOLIDWORKS software. The purpose of the tool is to meet the information we use to create our designs is same as the information we provide to manufacturing.
Why Tolerance Stack-Up Analysis
When we designed a model to its nominal size in SOLIDWORKS and going for manufacture. It might not be the exact nominal size we have created, whatever the manufacturing technique we use it might not fit. We will find the tolerance stacked up through the components, it will either too big or too small and will end up with a clearance issue.
TOLANALYST
The TolAnalyst or tolerance Stack-up analysis tool automatically checks the effects of tolerances on parts and assemblies to ensure consistent fit of components and to verify the Maximum/minimum worst-case and RSS results before a product goes into manufacturing.
Where to Find:
From DimXpert Manager > TolAnalysis (or) Command Manager > SOLIDWORKS
Add-ins > TolAnalysis
If you want to run TolAnalyst, every single part that going to involve in tolerance analysis study must have already ran a DimXpert on it.
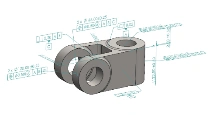

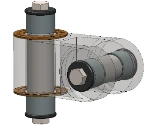
Example: Here with, I want to make sure that above components have enough clearance and tolerance. That this thing is going to function properly before going to manufacturing using Tolerance Stack-up Analysis.
Step 1: MEASUREMENT
Establish the measurement, which is a linear distance between two DimXpert features.
Measure the distance between the DimXpert featured parts you want to involve in TolAnalyst Study to its (Center or Min/Max distance).
Example: In this scenario, I want to measure the clearance between the Knuckle and Pin Shaft both the parts are involved to DimXpert feature.

Step 2: ASSEMBLY SEQUENCE
Select the assembly order of the parts to establish a tolerance chain between the two measurement features “simplified assembly”.
Example: First select the Base part of the assembly, once selected the remaining part goes to wireframe and add the components in sequence like how the assemblies are put together in production.


Step 3: ASSEMBLY CONSTRAINTS
Define how each part is placed or constrained into the simplified assembly.
Constraints are used to define the relationships between components within an assembly. Constraints ensure that components are positioned and oriented correctly relative to each other.
Example: The base part shows as constrained, because it is fixed as the origin part. The remaining relative part needs to be constrained to the assembly using constrain callouts box before running the study.


Step 4: ANALYSIS RESULTS
Evaluate and review the minimum and maximum worst case tolerance stacks and RSS.
TolAnalyst results are displayed visually in the graphics area. Warning messages appear if there are potential problems with the setup and evaluation.
Example: Once the assembly is set up with tolerances, run the TolAnalyst. SOLIDWORKS will automatically calculate the maximum and minimum dimensions for each part based on the defined DimXpert tolerances.


If necessary, we can modify the Analysis Parameter options under Min/Max Contributors. By double-clicking the listed dimensions and tolerances to modify their tolerance values and click Recalculate to compute new results.


After the analysis is complete, we can export the results in a report format with various parameters such as:
Worst-case stack-up: Max deviation in assembly dimensions considering all possible combinations of tolerance values.
RSS (Root Sum Square) stack-up: Calculates the root sum square of all tolerance variations to determine the overall variation in the assembly.
Individual part variations: Information on how each part’s tolerance contributes to the overall variation in the assembly
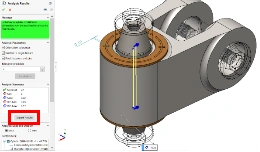
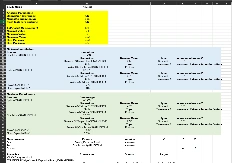
Benefits of TOLANALYST:
1.Tolerance Stack-Up Analysis: Predict how variations in component dimensions and tolerances will affect the overall assembly’s performance and functionality.
2.Identify Critical Dimensions: Identify critical dimensions and tolerances that have the most significant impact on product performance, reliability, and manufacturability.
3.Optimize Tolerances: By simulating different tolerance scenarios, optimize tolerances to meet performance requirements while minimizing manufacturing costs.
4.Reduce Scrap and Rework: By identifying potential issues early in the design phase, reduce the rework due to dimensional variations during manufacturing.
5.Improved Quality and Reliability: By ensuring the product quality and reliability, leads to customer satisfaction and reduced warranty claims.
Have questions or need assistance? Feel free to reach out!
Email: mktg@egs.co.in
Phone: +91 94454 24704
- Get link
- X
- Other Apps
Comments
Post a Comment